The Quick Online Service
We provide you with a comprehensive range of services, including technical consultation, feedback, application for returning to the factory, and on-site maintenance. We will offer you the services in the fastest and most professional manner.
Service Promise:
During the warranty period, a certain repair fee will be charged if the damage is caused by the following reasons:
– Damage to the machine resulting from mistakes in use and unauthorized repairs and alterations.
– Machine damage caused by fire, flood, abnormal voltage, other natural disasters, and secondary disasters.
– Hardware damage due to man-made falls and transportation after purchase.
– Damage to the machine arising from operation not in accordance with the user manual provided by our company.
– Failure and damage caused by obstacles other than the machine (such as external equipment factors).
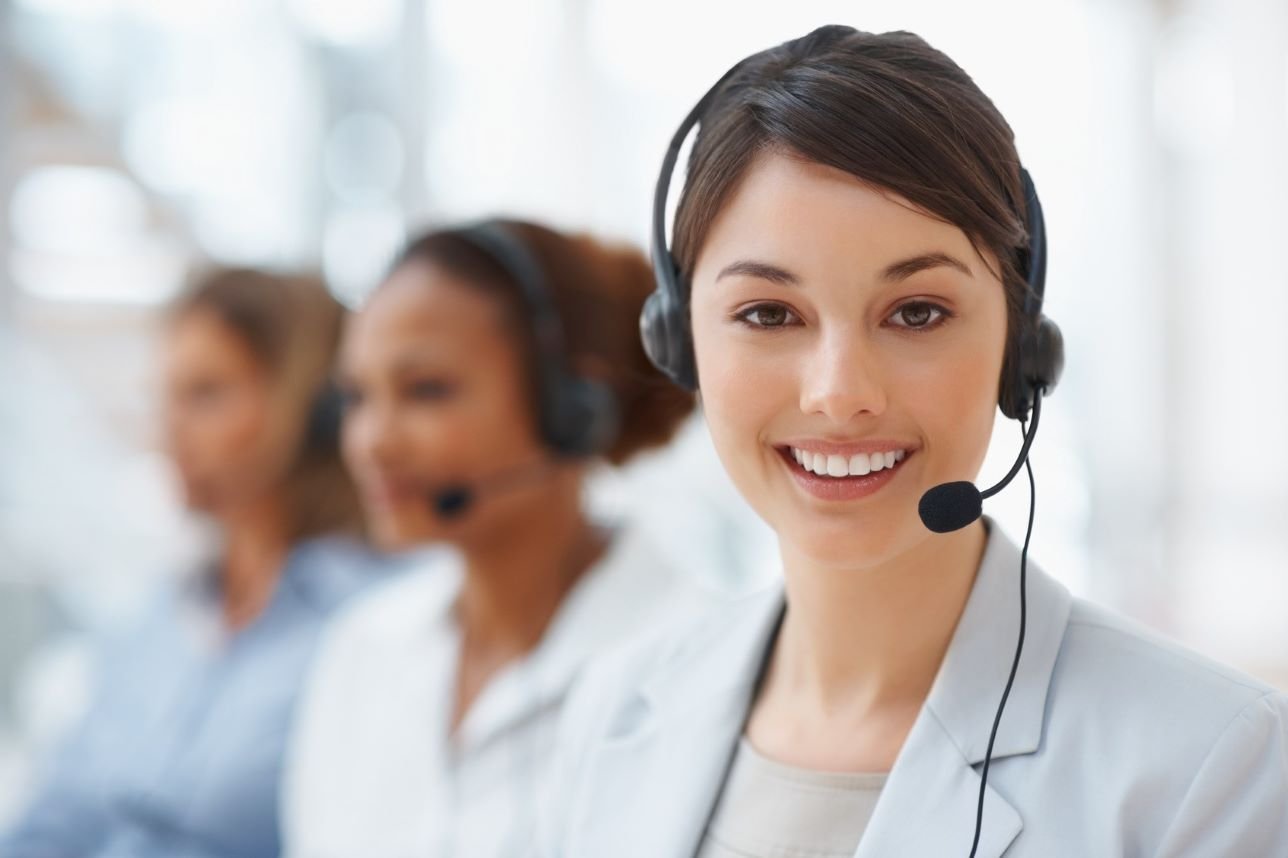
Frequently Asked Questions
Find answers to commonly asked questions about our products and services.
How to check whether high speed running of the elevator is normal?
1. The autotuning of the hoistway height was successful.
2. Ensure that no one is in the car, on the car top, in the hoistway or in the pit. All hall doors and car doors should be closed, and the safety circuit and door lock circuit should be normal.
3. Operate the elevator to run at a low speed to the middle floor in the machine room. Switch to automation, issue a single – floor command in the controller, and check the feedback speed, leveling signal, and traction machine to see if the elevator can start, accelerate, decelerate, level, and stop properly. If there is an abnormality, adjust the relevant parameters.
4. After the elevator runs normally on a single floor, issue a double – floor command in the controller. Check the feedback speed, leveling signal, and traction machine to see if the elevator can start, accelerate, decelerate, level, and stop properly. If there is an abnormality, adjust the relevant parameters.
5. After the elevator runs normally on double floors, issue a multi – floor command in the controller. Check if the elevator can start, accelerate, decelerate, level, and stop properly. If there is an abnormality, adjust the relevant parameters.
6. After the elevator runs normally on multiple floors, operate it to run at multi – floor speed to the top and bottom floors and check if it is normal.
7. After normal running at the top and bottom floors, check whether the effective distance of the up and down forced – deceleration switches complies with the standards. Then, check if the elevator hits the top or bottom when arriving at the top and bottom floors. If there is an abnormality, adjust the distance of the up and down forced – deceleration switches.
Precautions for Hoistway Autotuning of the Elevator.?
To prevent the autotuning speed from being too high, the recommended value of P1.13 is 0.100m/s. High – speed operation may easily lead to the loss of pulse counting, and an abnormal position may cause a fault and a stop. After the hoistway autotuning, if the position of the magnet vane or the forced – deceleration switch is adjusted, perform the hoistway autotuning again.
How to check whether the encoder or PG card is in good condition or not?
You can conduct a test run of the system in an open – loop mode as follows:
1. Set P00.00 = 1 (open – loop vector).
2. Set P20.07 = 4 (Enable the encoder pulse – counting function).
3. Monitor P17.18 (encoder pulse: Hz).
4. Then compare P17.18 with the running frequency (Press “shift” six times, and the running frequency will be displayed). If P17.18 is not equal to the running frequency, it indicates that there is a problem with the PG card or the encoder itself. Try replacing them to identify the issue.
How to select an inverter with a double – sided panel?
When using double – sided modules, the following points should be noted when selecting an inverter: Firstly, avoid overmatching. Bifacial modules can sometimes increase power generation by 20% – 30%, meaning an increase in output power. It is recommended that the modules and inverters be configured at a ratio of 0.9:1. Secondly, when the power of the module increases, only the current may increase, while the voltage will not. Therefore, it is necessary to select an inverter with an input string current greater than 12A.
How to Reasonably Select Inverters with Different System Voltage Levels?
With the increasing pursuit of power generation efficiency in photovoltaic power stations, the voltage on the DC side of these stations has been gradually increasing. In the early days, inverters with a maximum DC voltage of 600V have been replaced by those with a 1000V voltage, and this has even risen to 1100V.
Undoubtedly, the high voltage on the DC side of the photovoltaic system can reduce line losses and improve system efficiency. Therefore, the current 1100 – volt system scheme has become the top choice for large – scale photovoltaic power stations. We believe that most distributed photovoltaic power stations, such as household photovoltaic systems or those installed on the roofs of various buildings, are closer to people’s daily lives. They are usually connected to the user – side power grid with a low access voltage. Besides pursuing the power generation efficiency of the photovoltaic power station, safety is of greater importance.
Therefore, a system scheme with a voltage below 1100V should be adopted whenever possible. High – efficiency inverters with a low starting voltage and a wide MPPT (Maximum Power Point Tracking) range should be selected.
What is the function of AFCI?
In the entire photovoltaic system, the voltage on the DC side is usually as high as 600 – 1500 VDC. Due to reasons such as loose connections, poor contacts, damp wires, and insulation ruptures, it is very easy to cause DC arcing.
The high temperature generated by the arc can easily lead to a fire when adjacent substances reach the ignition point. That is to say, DC arcing is a potential safety hazard.
The AFCI functions by identifying the arc – fault characteristic signals in the circuit. Before the arc fault develops into a fire or a circuit short – circuit, the AFCI will disconnect the power supply, which greatly enhances the system’s safety.
What is the function of I – V curve scanning?
In case of shielding and poor connection in the solar plant, the I – V curves of panels will be abnormal. The system can judge the problems in the solar plant by detecting the I – V curves of the photovoltaic array and automatically provide relevant operation and maintenance schemes. Compared with traditional maintenance methods like visual observation, this approach is more accurate and faster. Moreover, it is more convenient and economical as there is no need to purchase expensive operation and maintenance equipment.
What causes Low power generation in the solar inverter system?
It is mostly caused by improper design, unreasonable string matching, and incorrect parameter settings (safety regulations, MPPT working mode), etc. Possible Causes and Solutions:
1. PV panels are blocked by buildings, trees, poles, wires, front – row components, etc. — Investigate the site, fully consider surrounding shielding factors, remove removable obstructions, and optimize the series – parallel connection mode.
2. PV panels are covered with fallen leaves, bird droppings, dust, dirt, plastic bags, etc. — Clean the PV panels in time.
3. Different types and specifications of PV panels are mixed. — The same type of PV panels should be connected into one or more groups, and multiple groups should be placed under the same MPPT.
4. The power distribution in the series is unreasonable, with the power mainly concentrated on one of the MPPT channels. — Distribute the power evenly to the two MPPT channels.
5. The inverter safety regulations are set incorrectly, or the MPPT working mode is set incorrectly. — Set the safety regulations correctly and select the corresponding MPPT working mode according to the front – end series connection mode (the parallel mode is rarely used; for details, consult our technical personnel).
6. The diameter of the cable used from the inverter to the parallel network point is too small and the distance is too long. The cable material is aluminum core wire, resulting in larger line losses. — Choose a cable with a larger wire diameter, select copper – core cables, and plan the wiring path reasonably.
Does INVTAR medium voltage VFD support the motor temperature sensor?
Yes. INVTAR MVD supports the motor temperature sensor terminals. One solution is to use a temperature controller to collect the signal, and the information is shown on the controller. The other solution is to use INVTAR PLC + PT to collect the signal, and the information is shown on the HMI.
Does INVTAR medium voltage VFD have grid line power momentary interruption and the MVD not – stop function?
Yes. INVTAR MVD has this function. When the grid line power is off briefly for 0.1s – 5s, the MVD can continue to drive the motor without a fault.
What parts does the INVTAR explosion proof inverter contain?
It usually includes the inverter unit, explosion – proof enclosure, backplane, heat – pipe radiator cooling fan, and optional accessories such as EMC filters, reactors, etc.
What’s the difference between a photoelectric encoder and a magnetic encoder?
Photoelectric encoder: It has high accuracy but cannot be used in environments with high temperature, vibration, or oil contamination. Magnetic encoder: Its accuracy is relatively low but it can adapt to the rugged environments with high temperature, vibration, or oil contamination.
What is the purpose of the frequency swing of the VFD in the textile industry?
It is mainly used to prevent silk folding. When the winding diameter reaches a specific value, the trajectory of the first repeated action will achieve a coincident effect. If too many yarns overlap, silk folding will occur, creating potential hazards for the unwinding in the next process. Therefore, it is necessary to add a swing frequency, which is equivalent to introducing appropriate disturbances during the regular operation process.
Why does the textile industry often change speed in the spinning process?
Tension significantly affects the formation of spinning, and spindles of different sizes have diverse tension requirements. Hence, distinct speeds should be set in accordance with different processes and spinning stages to precisely meet the tension requirements.
What are the Precautions for VFD – controlled Permanent Magnet Synchronous Motors in the Textile Industry?
Attention should be paid to anti – reversal at the starting moment of the permanent magnet synchronous motor, and also to the demagnetization of the synchronous motor caused by high ambient temperature.
What problems should be noted in the textile industry?
In textile production sites, high temperature and humidity can block the cooling air ducts of variable – frequency drives (VFDs) and damage the fans. At chemical fiber textile sites, oil stains and corrosive substances can easily generate frictional static electricity. At printing and dyeing sites, attention should be paid to moisture prevention and corrosion protection.
Why Is There a Leakage Current Problem?
When the variable – frequency drive (VFD) is not in use, the leakage current is generally small. When the VFD is in operation, since the power module of the inverter switches at a high speed, there are high – order harmonics in the output current. Due to the inductance between the cable and the ground as well as between the cables, a large leakage current (up to 10 times that when the VFD is not in use) is generated.
Why does the VFD stop during operation when large motors start simultaneously?
When a motor starts, a starting current corresponding to its capacity will flow, and the transformer on the stator side of the motor will experience a voltage drop. When the motor has a large capacity, this voltage drop will have a significant impact. The VFD connected to the same transformer will make a judgment of undervoltage or instantaneous stop. As a result, sometimes the protection function is triggered, leading to a stop.
Can I track my order?
Yes, once your order has been shipped, you will receive a tracking number via email. You can use this tracking number to track the progress of your shipment on couriers website.